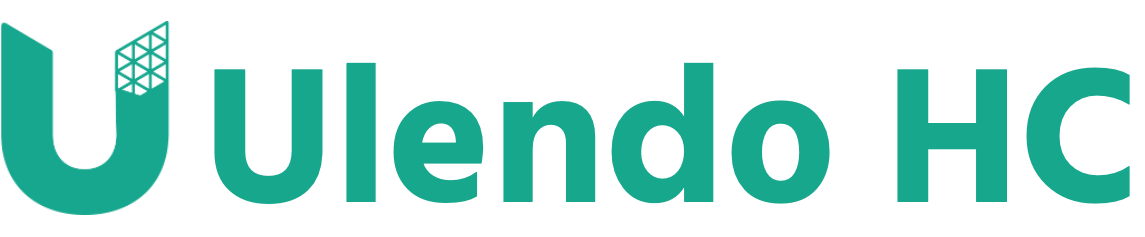
Heat compensation for LPBF printers
Quality improvements that matter:
88% reduction in residual stress
50% reduction in mean deformation
26% reduction in max deformation
Ulendo HC is a software module that optimizes the laser path of a laser powder bed fusion (LPBF) printer. Powered by Ulendo's patent-pending algorithm, Ulendo HC cuts heat-induced distortion in half without adding significant printing time. We work with LPBF printer manufacturers to integrate the plugin into a specific printer model and with process control software providers for LPBF machines to include the plugin as a valued feature of their software platform.
NOW AVAILABLE as a
Standalone Desktop Application
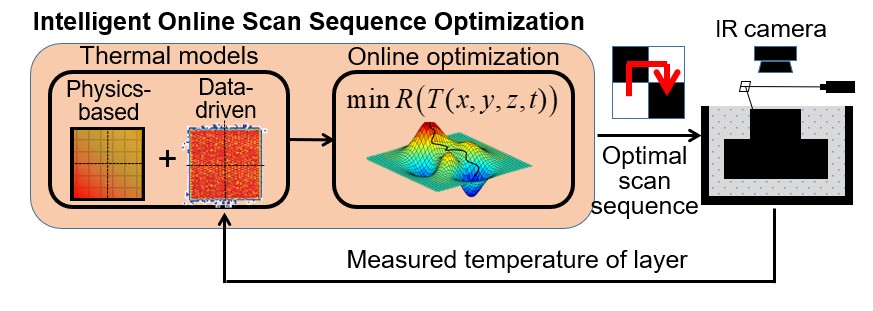
Improve
productivity
Ulendo HC automatically determines a laser scan path that reduces heat-induced distortion, thereby relieving the engineer of that aspect of the build process.
Avoid
failed parts
The significant reduction of heat-induced distortion leads to less failed parts that have to be discarded, thereby saving time and costs.
Reduce
post-processing
The significant reduction of heat-induced distortion reduces the time and costs of stress reduction post-processing.
Improve
printer ROI
By enabling more high quality parts to be printed, the LPBF user derives a higher ROI on their investment in an LPBF printer.
FAQs
Find answers to common questions about our product and its benefits.
Ulendo HC is a software module accessed through the user interface of an LPBF printer’s process control system. Using a patent-pending algorithm, an optimal laser scan sequence path is generated based on the material properties, laser speed and previous layers of the geometry. The required inputs are part geometry, materials properties (e.g., heat conductivity, heat capacity, density) and process parameters (e.g., laser power and scan speed).
Ulendo HC charts an optimal laser path that reduces heat-induced distortion by half and residual stress by up to 9x. This enables the build engineer to spend less time on scan strategy and more on other parameters that optimize the efficiency and quality of the printing process. Significantly reduced part distortion and residual also reduces the amount of post-processing time and expense. It also reduces the need for support structures or the risk of a recoater crash due to part distortion during the build process.
The Ulendo HC algorithm has been designed with a "plug and play" approach, and the Ulendo team can collaborate quickly with the engineering team of a process control software platform or a manufacturer of LPBF printers to leverage the power of this technology for your end customers. Essentially, we map from the printer, the required inputs for the plugin: part geometry, materials properties (e.g., heat conductivity, heat capacity, density) and process parameters (e.g., laser power and scan speed). Get In Touch for implementation details.
The software is also available as a standalone desktop app.
Yes, Ulendo HC is available as a software modle add-on to Dyndrite's LPBF Pro software platform. https://www.dyndrite.com/lpbf-product
Consult our website for our Early Adopter Program with Dyndrite: https://www.dyndrite.com/lpbf-product
More integrations to come in 2025.
Yes. It is available on an a annual subscription basis starting at $2,500 per printer based on the printer's build volume. A 50% Early Adopter Program discount is available through March 31, 2025.
While optimizing the path to minimize heat-induced stress and distortion, that optimized laser path increases the print time for the part by less than 3%. However, because of the reduction in failed builds due to heat distortion, Ulendo HC users can expect significantly improved productivity, less material waste, and reduced post-processing time over the course of a series of builds.
When included in a process control software platform, the cost of Ulendo's additional heat compensation plugin will be determined by the provider of that software platform. Stay tuned later this year for a list of software platforms to which Ulendo HC has been integrated.
For manufacturers of LPBF printers, Ulendo's goal is to drive meaningful value for you and your end users. Ulendo HC is licensed to the manufacturer on a simple volume-based royalty. Pricing varies depending on the underlying software platform. Get in Touch to schedule a demo and discuss pricing on your LPBF platform.
The Ulendo HC desktop app is available on an a annual subscription basis starting at $2,500 per printer based on the printer's build volume. A 50% Early Adopter Program discount is available through March 31, 2025.
Early Adopter Program for Ulendo HC
Fill out the form below